How to Choose the Right Inventory Storage System for Your Small Shop or Business
What are the types of inventory systems?
Many different types of inventory systems are available to businesses, each with its advantages and disadvantages. The type of system you choose will depend on several factors, including the size and nature of your business, the amount of space you have available, and your budget. The most common types of inventory systems are:
Self-storage
Self-storage can be a great option for businesses with a small number of customers, as it allows them to eliminate overstock or supplies without having to take up extra space in the shop or office. However, for businesses with large customers, self-storage may not be the most efficient way to store inventory. It can also result in additional costs if not enough space for all the products. In such cases, investing in an appropriate inventory system that meets the specific needs of your business may be more beneficial and cost-effective in the long run.
Traditional warehousing
The benefits of traditional warehousing are that it is a more professional way to store inventory before shipping. However, starting in 2021, warehousing tenants will face a 10% rate hike, and business owners will be required to cover workforce expenses and additional space expansion costs. The drawback of traditional warehousing is that it can be expensive for small businesses due to the amount of work needed to keep track of inventory and supplies. On-demand warehousing platforms provide an alternative option as they help users find excess warehouse space but do not offer any fulfillment centers themselves.
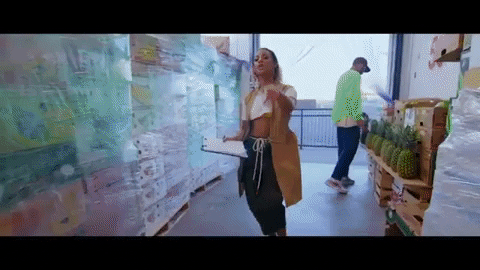
Third-party logistics (3PL)
Third-party logistics (3PL) is a process in which an external service provider takes on the responsibility of storing and moving inventory for a retailer. This process can offer many benefits, such as reduced storage and shipping costs, decreased responsibility for handling inventory, access to expert resources to deal with products, and faster shipping times. 3PL services can be more cost-effective for brands with consistent sales than setting up their warehouse. Furthermore, this service allows retailers to outsource their fulfillment processes without sacrificing product quality or control over production. Overall, 3PL is an ideal option for businesses looking to expand into physical retailing without the huge overhead costs associated with running warehouse operations.
Dropshipping
Dropshipping is a type of purchasing and inventory system used by retailers in which goods are not stored on-site or in warehouses. Instead, goods are shipped directly from the supplier to the customer. This reduces risk and improves cash flow for small businesses, as there is no need for a large inventory or fulfillment team. Furthermore, product quality and branding can be difficult to control with drop shipping, but it offers competitive pricing with razor-thin margins. Just-in-time inventory management is one approach to dropshipping that allows stock only to be sent when needed without storing it for long periods.
Self-fulfillment warehouse
A self-fulfillment warehouse is a location established by a retailer to store and manage their inventory. This type of warehouse gives businesses complete control over the fulfillment experience offered to customers and can help save costs in the long run. However, it requires a long-term lease agreement and may involve hiring personnel and investing in WMS software. Typically, self-fulfillment warehouses are best suited for established retail brands anticipating future growth. A self-fulfillment warehouse efficiently organizes and stores products securely while providing an experienced operational team that can easily fulfill orders even if business increases substantially.
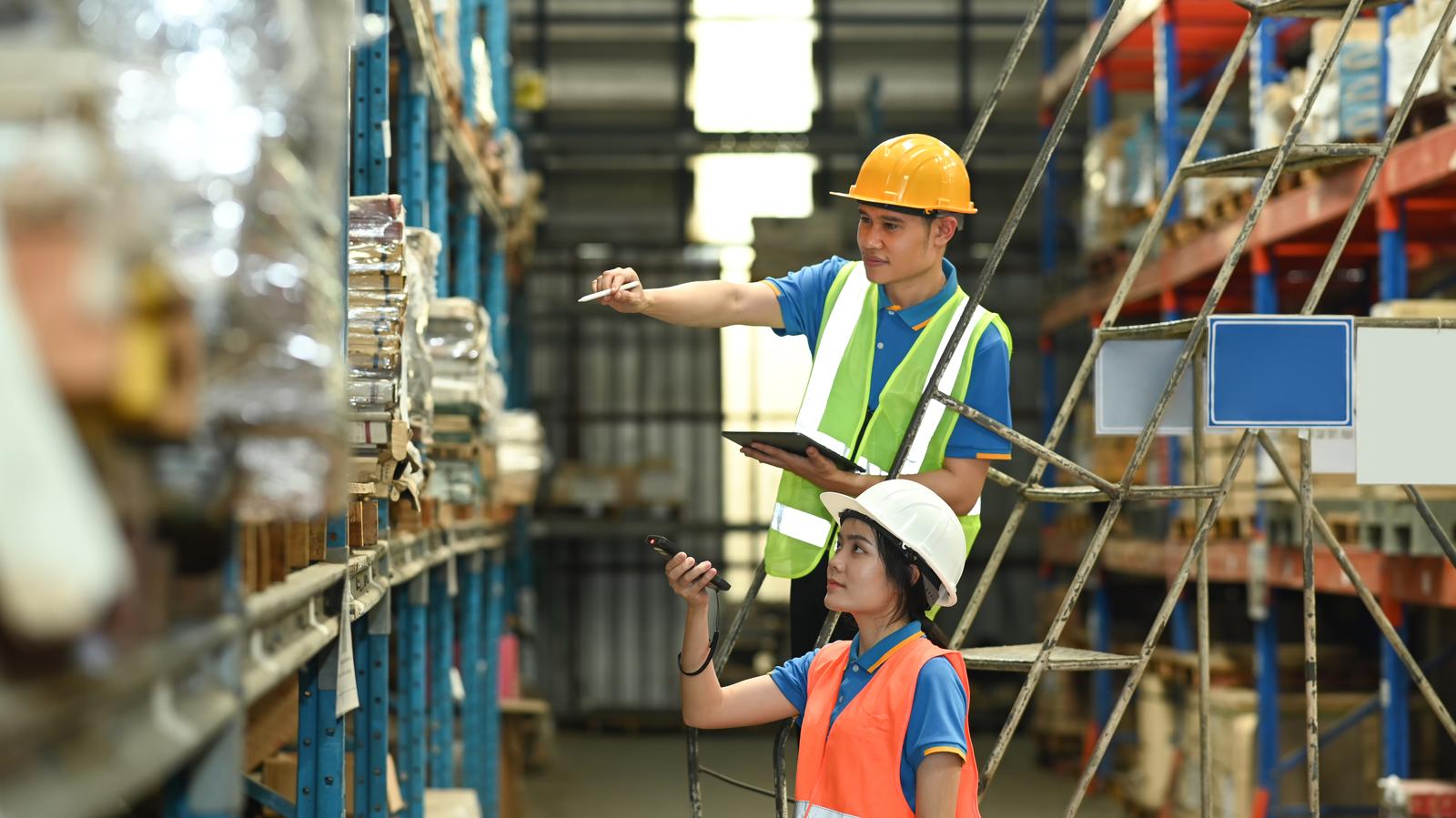
What are the factors to consider when choosing a storage system?
You need to consider many factors when choosing the best storage system for your home or office. With so many options on the market, it can be overwhelming to try and figure out which one is right for you. But don’t worry. We’re here to help answer the question lingering in your mind: how to set up warehouse inventory.
Here are some of the things you should keep in mind when shopping for a storage system:
Cost
The cost is important when choosing a storage system since it can include several factors, such as space, utilities, insurance, and inventory. Additionally, the average cost per month for a self-storage unit usually ranges from $100-$300. Those who may be looking into third-party logistics (3PL) providers may find these more expensive than central storage systems; however, this additional expense could bring with it added experience and personnel that would be beneficial. In addition, the higher cost comes with less safety stock, leading to increased costs to cover any unexpected spikes in demand. Central storage systems also tend to be less safe due to their lack of inventory which does not provide adequate protection against unexpected demand spikes.
Location
Location is important when choosing a storage system for inventory because it can help ensure that items are stored in the most efficient and accessible way possible. A central storage system is also beneficial, as it helps reduce the safety stock that needs to be kept in reserve. Alphanumeric combinations can identify specific rows, shelves, and exact bin locations for larger warehouses.
Space
Space is an important factor to consider when choosing an inventory system because it will limit the amount of inventory that can be stored. Self-storage may be a cost-effective option for small businesses, but it can only accommodate limited inventory. Warehouse storage is more traditional and organized but has space limitations. Outsourcing to a third-party provider can provide increased efficiency, shipment speed, and security at the warehouse; however, this option costs more than managing storage in-house due to these additional benefits.
Security
Security is important when choosing an inventory system because a central storage system can increase demand and put businesses at risk. Different inventory storage solutions, such as self-storage, traditional warehouses, and partnering with 3PLs, each come with security measures that must be considered when deciding. To ensure that the business is adequately protected from potential risks or losses due to theft or damage, it is important to select the right inventory system that best meets its needs.
Flexibility
Flexibility is important when choosing a storage system because it allows easy access to the drives from various points and provides flexibility in loading and unloading methods. Last-in, first-out (LIFO), and pushback racks are two popular unloading methods, allowing businesses to adjust their budget, space requirements, and spoilage concerns accordingly.
Accessibility
Accessibility is important when choosing a storage system because it affects the system’s efficiency. Systems such as First-In, First-Out (FIFO) or Last-In, First-Out (LIFO) use drive racks or hydraulic arms that allow easy access from different parts of the system. This allows for more efficient warehouse organization and use of space, which can result in less safety stock being needed. Additionally, these systems are often space-efficient and require fewer resources than other inventory systems.
Storage Conditions
Storage conditions are important to consider when selecting a store inventory system because it affects the safety and availability of products. Different unloading systems, such as last-in, first-out (LIFO) and first-in, first-out (FIFO), can be used depending on the needs of the business. Choosing a central storage system over drive-in racks or pushback racks may require less safety stock to be kept, but it also comes with its own set of risks that must be considered.
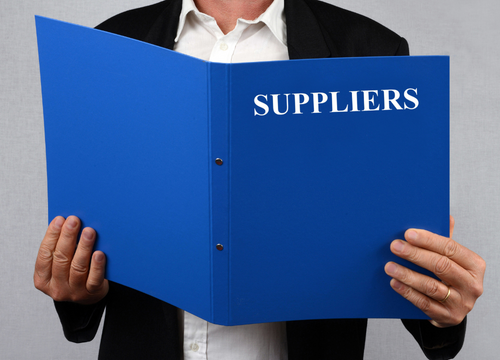
Suppliers
When choosing a supplier for an inventory system, individuals should consider the space available, budget, spoilage concerns, and unloading method (LIFO or FIFO). Additionally, they may wish to research different types of systems such as Rust, Unit Organizer Shelving Systems, and eBay’s options. Ensuring that the system is suitable for their small shop or business is also important.
Stock Control
Inventory storage is an important tool for businesses to keep track of their stock and inventory, regardless of location. With the help of inventory systems, businesses can better manage their products by categorizing, tracking stock levels, and monitoring the condition of stored items. This ensures that a business always has the right amount of stock on hand and can maximize efficiency to remain competitive in the market.
Packaging Materials
It is important to consider packaging materials when choosing an inventory system to optimize cube-fill rates and minimize travel time. The type of packaging material used can directly impact the speed and accuracy of a company’s supply chain and, therefore, must be chosen carefully to best suit the product mix and maximize space utilization. Additionally, accuracy must be maintained with product data to ensure efficient use of storage space.
Order Fulfillment
An inventory system is important when choosing a small shop or business storage system because it helps keep track of stock and prevents products from becoming outdated. It also ensures that orders are shipped on time, keeping the business organized and efficient. Additionally, with an inventory system such as eFulfillment Service, businesses only pay for the amount of space used, making it an economical choice. By utilizing the FIFO (first in, first out) approach with the right storage system for automated dropshipping, small businesses can streamline their order standard inventory management to improve efficiency.
Inventory Tracking
An inventory system stores and manages inventory within a shop or business. It can be either centralized at a single location, such as a warehouse, or multiple points throughout the business’s premises. Common methods of loading and unloading include Last In, First Out (LIFO) systems, which use drive-in racks or pushback racks, as well as pull and push unloading methods. Drive-through racks and flow-through racks offer multiple access points to the stored products.
Automation
Automating an inventory system can be beneficial for small shops or businesses, as it helps improve efficiency and accuracy. Automation reduces the time spent on manual data entry and eliminates costly human errors, resulting in lower costs overall. Automation also allows businesses to track their inventory more closely by providing real-time stock levels and purchase order updates. This can help ensure that they have enough safety stock available to meet customer demands while avoiding overstocking, which can result in wasted time and resources. In addition, automation streamlines the ordering process by enabling the automated reordering of items when certain thresholds are reached.
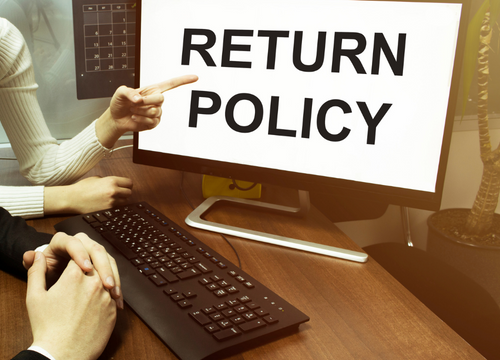
Return Policies
An inventory system is a system used to store and track the inventory of a business. It should be able to track and store items such as products, quantities, and SKUs. When selecting an inventory solution for a small shop or business, several factors should be taken into account, including space available, budget constraints, spoilage considerations (for food items), unloading stock options, dead stock removal process, tracking bestsellers rates, setting reorder points and counting the inventory regularly. Shopify POS can help manage warehouse and retail store inventories from the same back office quickly.
Training
Training employees on using an inventory system is essential for businesses to ensure efficiency, accuracy, and safety. A thorough understanding of how the system works allows employees to make informed decisions about when and how to store items. Training also helps ensure staff is familiar with any potential risks associated with different systems, such as those found in warehouses or self-storage facilities. Without proper training, companies may face additional inventory storage costs due to a lack of knowledge or experience, making it important for business owners to invest in educating their staff before deploying a new inventory system.
Ecommerce Integration
An inventory system is important for ecommerce businesses because it allows them to manage their stock levels, track bestsellers effectively, and set reorder points. It also helps with counting inventory and clearing out any deadstock. Having an efficient storage system in place can help to optimize supply chains and reduce waste. A good inventory system enables businesses to meet customer expectations, grow their business, and ensure customers receive the products they ordered.
Scalability
When considering an inventory system, scalability is an important factor. A business with limited space may not be able to accommodate a large amount of stock or have enough space to store goods awaiting purchase. By choosing a system that can be scaled up or down depending on the size of the business, businesses can ensure they have enough space and resources to run their operations efficiently. Additionally, a scalable inventory system will enable businesses to expand their operations as needed without having to invest in additional storage solutions.
Inventory Shrinkage
When choosing an inventory control, it is important to consider the possibility of inventory shrinkage. Inventory shrinkage occurs when a business experiences lost or stolen inventory and can be difficult to quantify due to its indirect cost. To prevent this loss, the right storage system should be chosen in order to limit access and ensure accurate tracking of items.
Shipping Fees
It is important to consider shipping fees when choosing an inventory storage system because these fees can greatly impact the monthly rate for using the system. The monthly storage fee is calculated by dividing the monthly fee by the number of days used, and different taxes will apply depending on where your inventory is stored. Additionally, your inventory may be suspended if a transaction fails due to insufficient funds in your bank account. Therefore, it is essential to factor in shipping and storage fees before selecting an inventory storage system.
Brand Management
When selecting an inventory storage system for a small shop or business, it is essential to consider brand management. An effective system for organizing and tracking store inventory is crucial to maximizing sales. It’s also important to ensure that the most popular items are easily accessible and not hidden away. Keeping a manual inventory of items, along with digital photos, can help businesses know exactly what their stock looks like at any given time. Investing in a storage system from a reputable brand that includes features such as unit warehouse storage organization and rust prevention can save time and money in the long run.
FAQs
Here are some of the most frequently asked questions about inventory management:
What is the inventory process?
The inventory process is critical in any business, as it helps keep track of products and ensure that a company has the correct inventory. Inventory reconciliation checks are conducted to verify this information. An appropriate inventory storage system is also important to manage and unload stock efficiently. There are two main types of unloading systems: Last-in first-out (LIFO) and first-in-first-out (FIFO). An effective storage system can help reduce theft and damage to products while allowing businesses to access their current inventory status easily. Different storage systems include Rust, Unit, Organizer Shelving, eBay options, and more. By choosing the right system for their specific needs, small shops or businesses can greatly benefit from efficient inventory management.
What is an inventory tracking system?
An inventory tracking system is used by businesses to store, manage, and track their inventory. The two main types of systems are last-in, first-out (LIFO), and first-in, first-out (FIFO). Factors such as space availability, budgets for storage solutions, and spoilage concerns related to certain items being stored too long or not kept in optimal conditions must be considered when selecting an inventory tracking system. Systems like Rust Inventory Storage System or UNIT Organizer Shelving may be the ideal solution for small shops and businesses looking for an efficient way of managing their stock. Additionally, those looking for more cost-effective alternatives could consider using eBay’s Marketplace Inventory System or other third-party services.
What is warehouse inventory management?
Warehouse inventory management is an important part of many businesses, as it helps to track and manage inventory accurately. This reduces the chances of errors and can make operations more efficient and cost-effective. Automation can also be easily incorporated into warehouses via warehouse management software (WMS). With this software, retailers have complete control over the fulfillment process, which they can deliver directly to customers. Although there is a significant initial investment in setting up a warehouse, it may be more cost-effective in the long run than using a third-party logistics (3PL) provider. For brands planning for long-term growth, self-fulfillment warehouses are often best suited.
Do you need to track inventory trends?
The benefits of tracking inventory trends include identifying which products are the most popular, making better decisions about stock levels, and utilizing affordable inventory management software with features to track these trends. Knowing which items are bestsellers can help businesses make more money as they can keep those items close at hand.